Digital evolution in shipbuilding: expert interview by Maritime Reporter
Greg Trauthwein, editor of the Marine Link magazine and Maritime Reporter TV, the flagship publication of the maritime sector, interviewed Alma’s expert in the name of Philippe Rouzeau, to discuss the digital evolution in shipbuilding and understand how to make shipyard complex shapes cutting efficient.
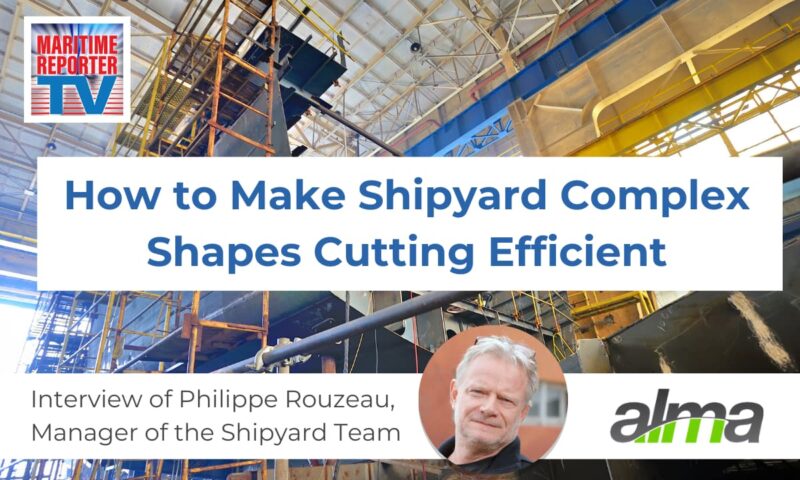
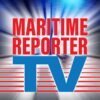
Greg Trauthwein : Philippe, to start, can you give a brief career background with insights on your current role at Alma.
Philippe Rouzeau : I started at Alma 35 years ago, managing CAM projects, notably with Les Chantiers de l’Atlantique, Alma’s first shipyard customer, who sought a nesting engine to reduce material costs.
After a few years in project management, I moved into business development, supporting Alma’s global expansion through subsidiaries and resellers.
All this time, the shipyard market remained a critical focus for Alma, even as it remained a niche sector. With the support of local subsidiaries, we implemented our CAM solutions in major shipyards across Europe, India, and the US. I and my colleagues had collaborate with major customers including Fincantieri (Italy), Meyerwerft (Germany), Lürssen (Germany), Cochin Shipyard (India), Larsen & Toubro (India) or Bath Iron Works (USA).
With a strong experience in the naval industry, I’m now the Head of the Shipyard team at Alma. My role is to help shipyards to digitalize their processes and integrate efficiently our Almacam solution into their environment.
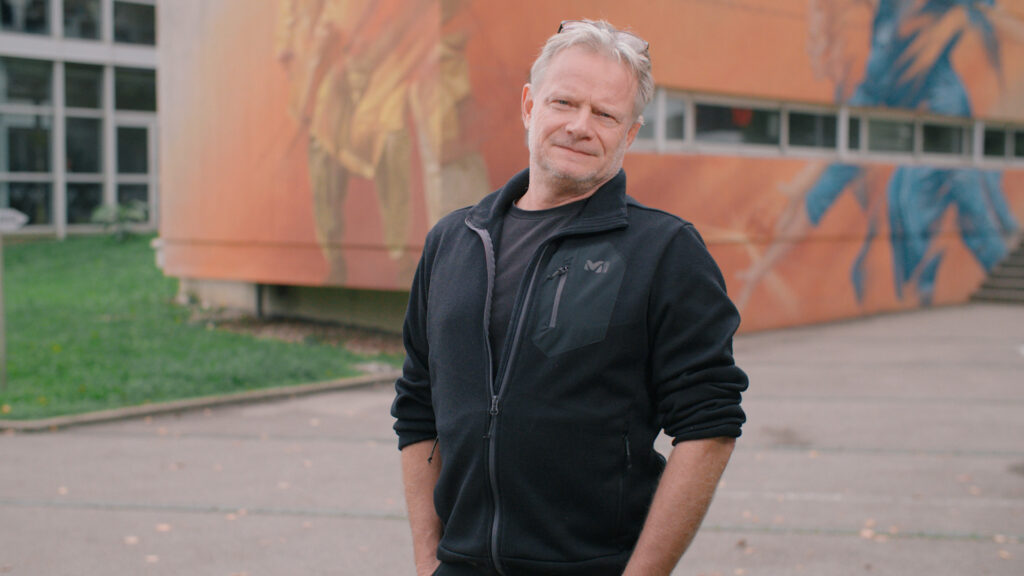
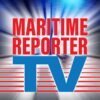
Greg Trauthwein : I’ve been covering the shipbuilding market for more than 30 years, and as you know, there is a broad gap among shipbuilders in terms of the uptake of modern CAD/CAM technologies in the name of efficient production.
How much of Alma’s business is maritime, and when you look at the shipbuilding market wholistically, broadly speaking where would you place the entire sector in its maturity in this regard as compared to other markets you serve?
Philippe Rouzeau: At Alma, the shipyard and offshore market represents approximatively 20% of our market. Compared to the whole sheetmetal market, I think you are right: shipbuilding market is a bit conservative regarding modern technologies but this can be easily explained.
The first reason is that a shipyard must keep and continue to use its CAD/CAM solution for the ships or series of ships that have been already built, sometimes for tenths of years. This for maintenance and traceability constraints. Shipyards cannot afford to use two CAD/CAM solutions for the same project. As a result, they adopt a new CAD/CAM solution when they launch a new project, that does not happen every day.
But the main reason is that the adoption of a new CAD/CAM solution, however effective it is, impacts a lot of people in the organization of a shipyard:
- the IT department is of course involved in integrating the system into the IT environment,
- the design (CAD) department is involved in providing data for the CAM,
- the “methods” department is involved for all technical specificities linked to naval domain,
- the workshops are impacted for the control of cutting machines.
Thus, it is not enough to propose an innovative solution, even reducing material costs or controlling efficiently the cutting machines. It is necessary to work with all teams from these departments in order to integrate the CAM solution into the overall environment of the shipyard.
Integration means:
- Communication with the different design or management systems (MRP, MES, CAD ),
- Control in the most automated way possible the specific machines equipping the shipyard.
To make it work efficiently, all these expectations require a strong expertise.
When you purchase a powerful CAM solution, the return on investment is typically just a matter of weeks or months. In any case, that's less than a year.
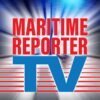
Greg Trauthwein : As I think you can attest, one hurdle in getting shipyards to invest in new technology is balancing the cost with the Return on Investment. I know that no two shipyards are alike, but for those watching that are considering an investment in new automated cutting systems, can you provide insight on the efficiencies they can expect to gain?
Philippe Rouzeau: The main gain a shipyard can expect by using a powerful CAM solution is the reduction of material cost. Let’s try to make an estimate.
For a matter of logistic, a shipyard uses to work per block. So let’s take parts with usual thickness in shipbuilding projects, 20 mm or 1 inch, from one block.
For such thickness, we may have 400 to 500 different parts (with complex shapes) to nest ; this can lead to approx. 20 nestings in a standard sheet format (10 m x 4 m).
In such a case, several benchmarks we did in the past showed we save 1 or 2 sheets, meaning about 10% reduction of wastes. But we cannot expect such wins for all thicknesses because of the number of parts to nest is reduced and do fill so many sheets. So, let’s take 4% wins ratio in average for all thicknesses.
If we make a projection on a complete cruise vessels of 30.000 tons, with a steel prize of $800 per ton, we can calculate a win between $900.000 and 1M$ wins.
▶ I let you read this article we published recently : it simulates the savings in materials and costs that can be achieved with efficient nesting.
So, as you can easily understand, when you purchase a powerful CAM solution, the return on investment is typically just a matter of weeks or months, and in any case, that’s less than a year.
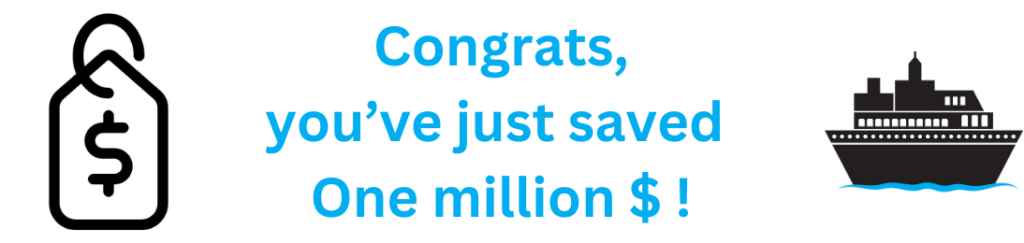
Reducing material wastes not only saves costs but also decreases the environmental burden of producing new steel, which involves substantial energy consumption and CO2 emissions. But material wins are not the only wins by using a new manufacturing solution.
- Thanks to technical functions and optimization algorithms such like cutting paths calculation, we reduce of machining time,
- Most of the time, our solution is fully automatized, meaning running in full batch mode: the programming time is also greatly reduced
These reductions of machining time or programming times are smaller than material wins but have to be considered in the choice of a new CAM solution.
Last but not least, a new CAM solution is not only chosen for its intrinsic efficiency. As we have talked about, it has to be fully integrated in the informatic environment of the shipyard, to communicate in a seamless way with CAD, MRP, … and to provide a complete traceability of produced data.
At Alma, this is what we propose and our added value also lies in the insights and guidance we offer to deploy our solution.
Read the full interview : how to make shipyard complex shapes cutting efficient
This article is an extract of a more detailed interview of Maritime Reporter TV. Look at this complete video to go in depth.