Why Offline Programming is a Game-Changer: 10 Lessons for Smarter Welding Robot Automation
10 Key Lessons to Understand the Power of Offline Programming for Welding Robots
If you’re currently using welding robots, or considering an investment in a robotic welding cell; it’s essential to evaluate the added value of an offline programming (OLP) software. Unlike traditional teach pendant methods, OLP allows you to program robots within a virtual environment, simulating movements and optimizing trajectories before any physical welding begins. More than just an alternative, OLP is a powerful component of modern automated welding machine software strategies.
In the 10 lessons below, we’ll explore why Almacam Weld, our dedicated robotic OLP solution, is essential for enhancing the performance, safety, and flexibility of your welding operations.
Lesson 1: Program up to 10 times faster than by learning
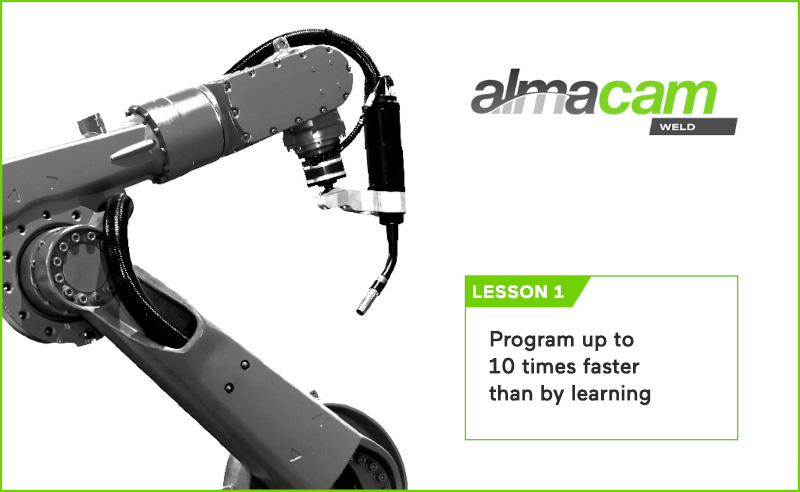
Conventional programming by learning requires moving the robot manually via a control unit—step by step, point by point—while recording trajectories, arc commands, and tool parameters. This process is labor-intensive, and it often takes one hour to program one minute of actual robotic welding time. For large or complex assemblies, the programming duration can multiply exponentially.
With offline programming, the entire workflow becomes faster and more efficient. Using a virtual scene and importing 3D models from CAD, weld paths are defined graphically and simulated without stopping production. Thanks to the automation and simulation features of Almacam Weld, programming speed increases dramatically—often up to 10 times faster than manual teach pendant methods. And this doesn’t even account for the massive time saved by keeping your robots continuously in production.
Lesson 2: Maximize your robots’ welding time
Every minute your robot spends idle is a minute of lost productivity. Traditional programming immobilizes your robotic welding machine, cutting into production time. In contrast, OLP enables programming to happen independently from the robot’s real-time activity.
With Almacam Weld, your robots keep welding while your engineers refine programs in parallel. Only minimal physical interaction is needed—usually limited to validation or minor adjustments—meaning you can maximize uptime, reduce bottlenecks, and extend the return on your automated welding machine software investment.
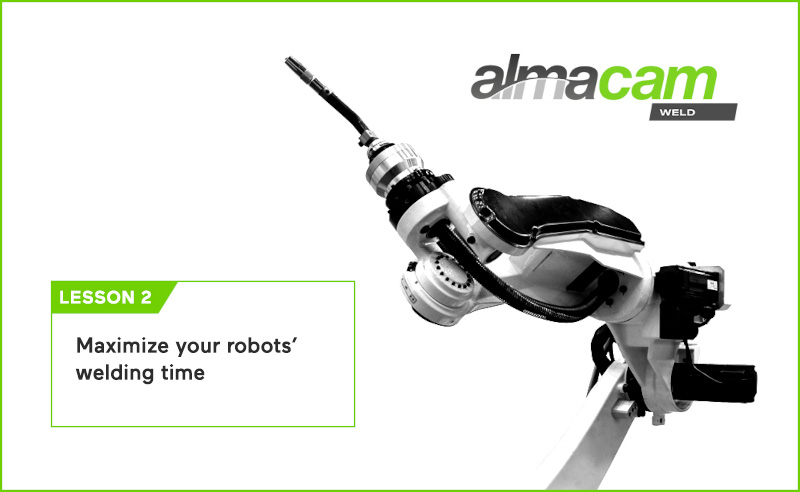
Lesson 3: Anticipate programming of your assemblies to weld as soon as they are designed
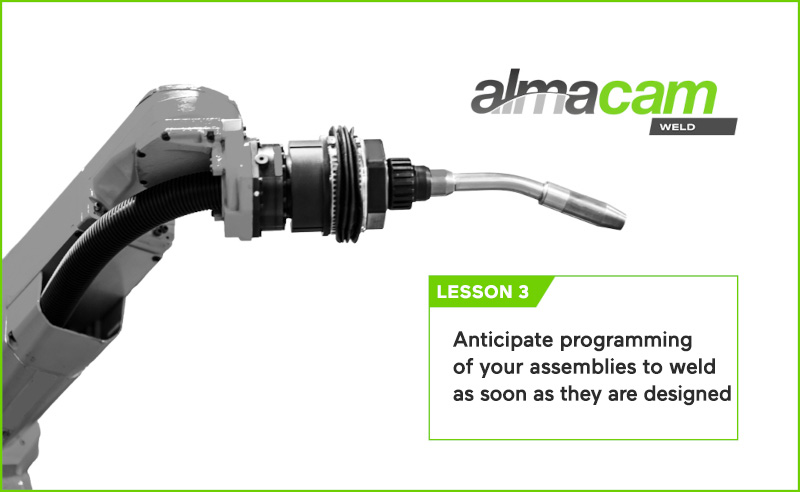
Teach pendant programming requires all parts, jigs, and fixtures to be built and available before programming can even begin. This delays your project timeline and ties up resources unnecessarily.
With Almacam Weld’s offline programming capabilities, you can start programming as soon as the CAD design is complete. No need to wait for physical components. This advanced design-stage integration accelerates your production planning and eliminates delays, allowing you to fine-tune programs well before assemblies reach the workshop.
Lesson 4: Improve safety for your operators and robots
Programming large assemblies with a teach pendant often forces operators into physically dangerous positions—standing at heights or working within hazardous areas of a live robot cell. It also exposes them to noise, fatigue, and distraction.
OLP reduces these risks entirely. With Almacam Weld, your programmers work comfortably and safely within the process planning or design office. Simulation-based programming not only protects your team but also minimizes the chances of damaging expensive robotic equipment during trial runs.
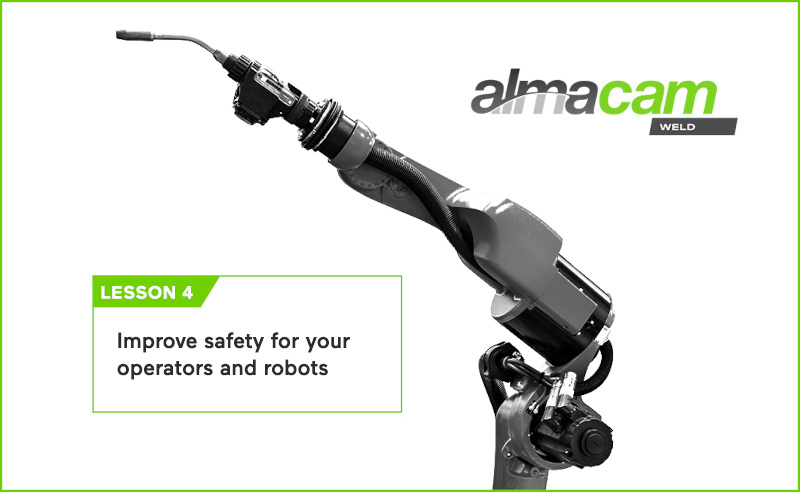
Lesson 5: Simulate the feasibility of welding your parts on the robot
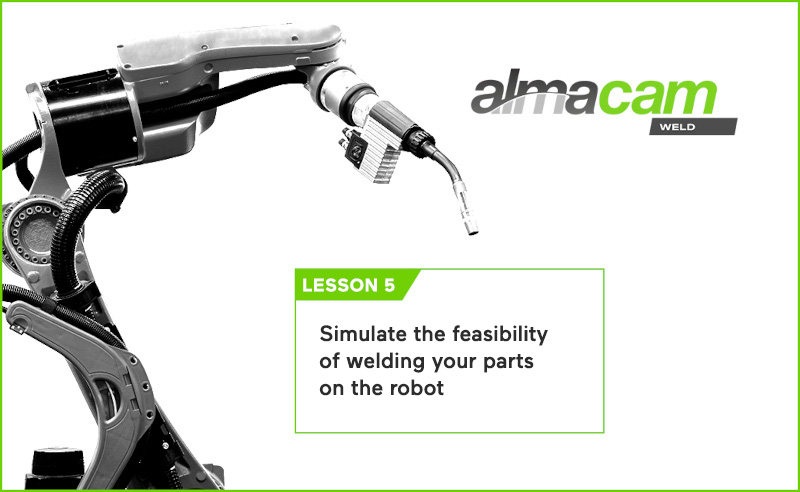
A major strength of OLP lies in its capacity to validate the feasibility of welds before production begins. Almacam Weld enables you to simulate full robotic movement, accounting for constraints like velocity, acceleration, joint limits, and singularities.
This real-time digital twin functionality helps you determine if a weld is achievable, identify accessibility issues, and visualize robot behavior. By simulating cycle times and robotic constraints early, you mitigate production surprises and increase planning accuracy.
Lesson 6: Improve weld quality
Weld quality is the hallmark of a successful robotic welding operation. With offline programming, torch angles, travel speeds, and part distances can be configured precisely according to Welding Procedure Specifications (WPS).
Almacam Weld goes beyond simple trajectory control by incorporating advanced welding logic—ensuring optimal bath angles and nozzle positioning throughout the process. These parameters, embedded directly in your OLP environment, improve consistency, reduce rework, and help you meet quality standards across your production lines.
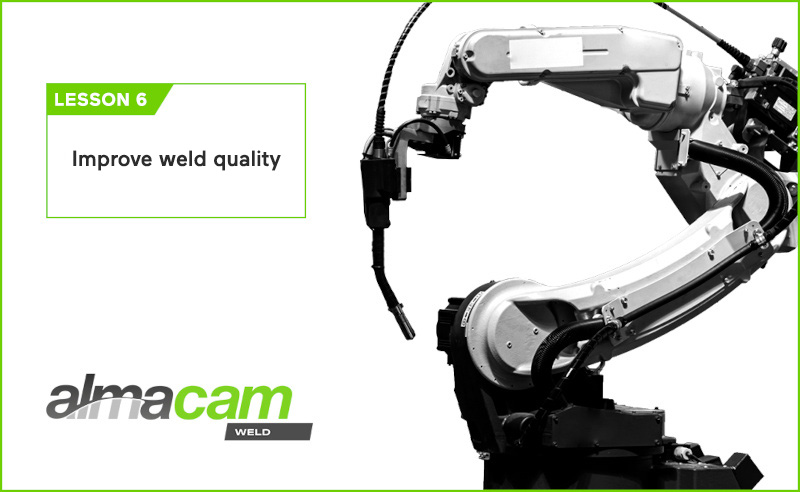
Lesson 7: Easily reproduce your programs on similar assemblies
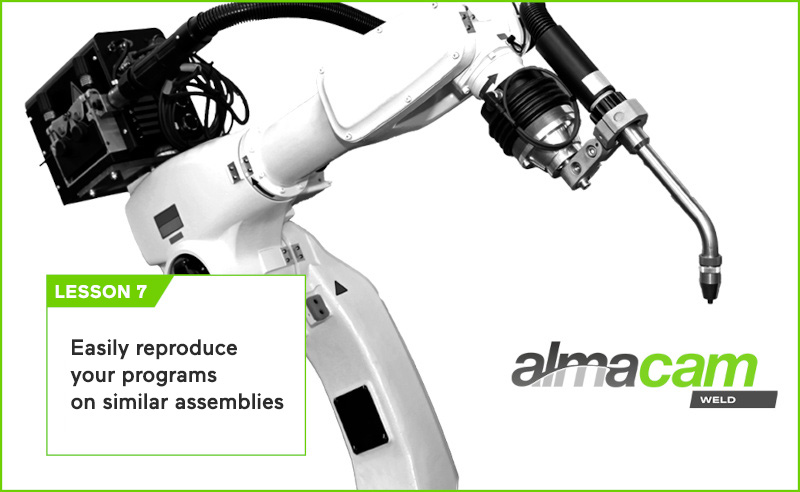
Manufacturers working with product families or modular parts often need to repeat similar weld sequences. Almacam Weld includes powerful features like duplication, symmetry, and cloning, allowing your team to replicate welding programs across similar assemblies without starting from scratch.
These functions accelerate deployment of new variants and dramatically cut programming time for product ranges—especially valuable in small-batch or high-mix production environments where flexibility is key.
Lesson 8: Prevent collisions between the robot and the assembly to weld
Collisions can result in costly downtime and damage to equipment. Thanks to Almacam Weld’s built-in collision avoidance algorithms, every movement in the robot’s trajectory is simulated and optimized to prevent interference.
This automatic trajectory recalculation, powered by intelligent OLP logic, ensures that the robot navigates safely around parts, jigs, and fixtures—even in densely packed cells. It’s an added layer of reliability for those seeking robust, intelligent automated welding machine software.
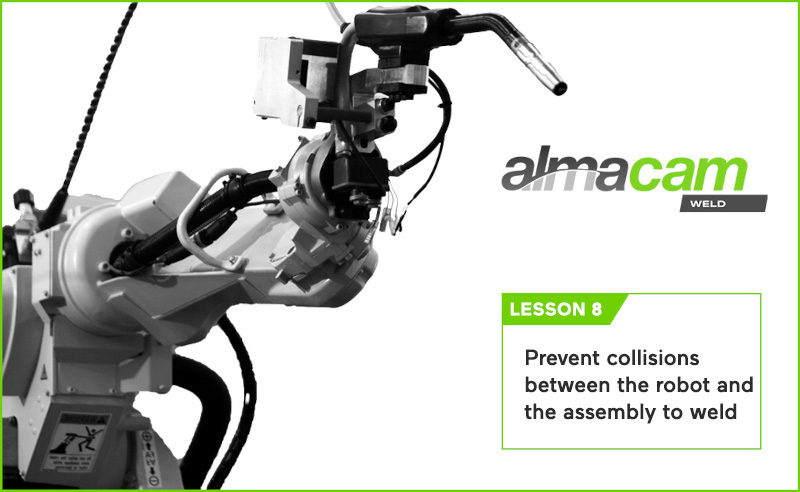
Lesson 9: Validate your tools before producing them
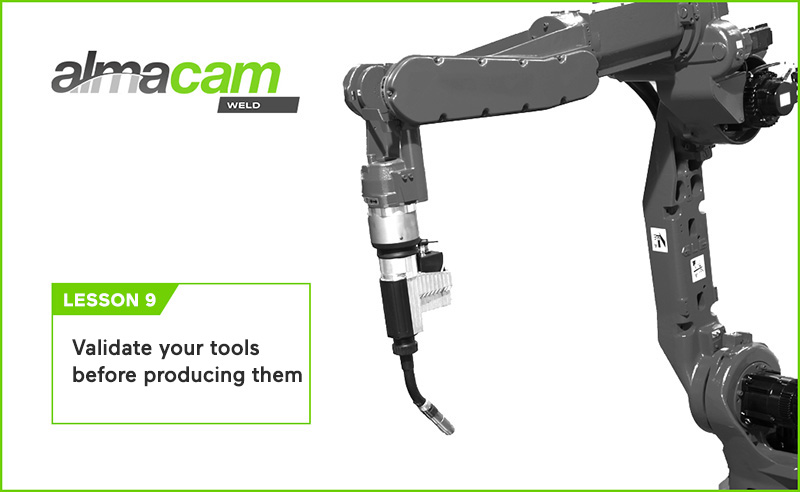
Tooling design mistakes are often discovered too late after fabrication. But with offline programming, you can simulate and validate tools before they’re built.
Using Almacam Weld, tool concepts are tested virtually alongside weld paths and robot behavior, helping you optimize both fixture design and workspace layout. By validating tooling early, you prevent costly redesigns and improve your Design for Manufacturability (DfM) workflow.
Lesson 10: Go beyond management of simple robotized cells
Almacam Weld is not limited to single-robot setups. It supports complex robotic cells, including multi-robot coordination, external axes, synchronized handling and welding robots, and more. This scalability ensures your OLP solution grows with your production needs.
No matter the size, brand, or complexity of your robotic cell, Almacam Weld adapts to it. As an independent OLP platform, it brings together powerful simulation, advanced automation, and universal compatibility—all in one smart automated welding machine software ecosystem.
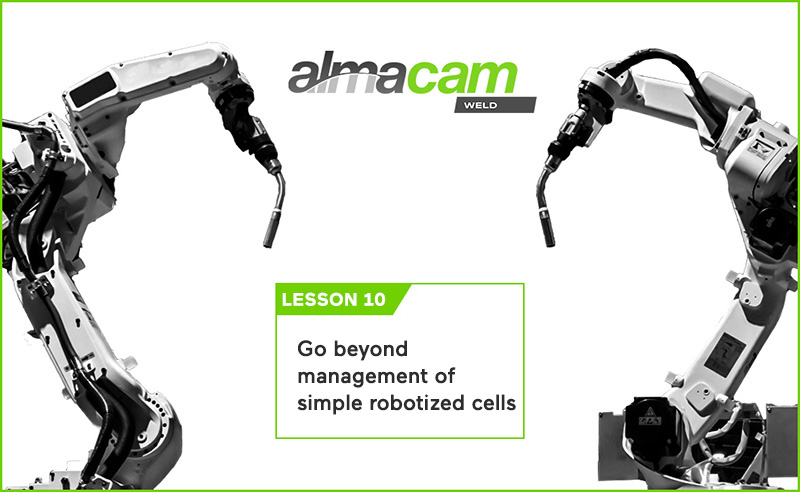
Ready to get more from your welding robots?
If you’re aiming to improve programming speed, weld quality, operator safety, and overall productivity, offline programming with Almacam Weld is your next step forward. From the first design sketch to final robot deployment, Almacam Weld brings automation, flexibility, and confidence to your welding operations without compromise.