Five Keys for Mastering Robotic Welding Programming: A Guide to Off-Line Success
Robotic welding programming using off-line programming software can revolutionize efficiency, delivering results up to ten times faster than traditional teach pendant methods. By eliminating the need to halt production for programming, OLP empowers manufacturers to automate even small production runs with unparalleled flexibility. However, successful integration of this approach demands meticulous planning and strategic implementation. Here’s a comprehensive guide to mastering programming a welding robot through off-line solutions.
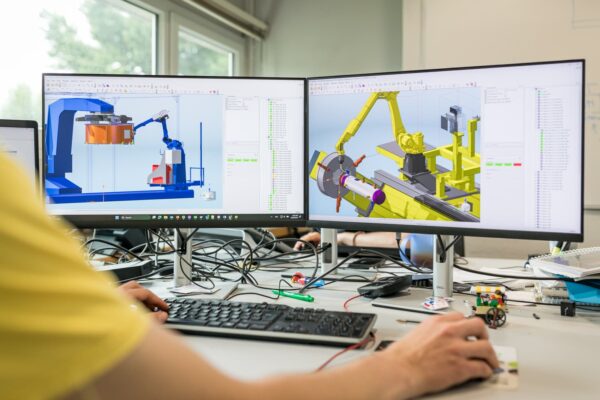
Incorporate Off-Line Programming Early in Your Robotic Welding Project
A strong foundation is essential for effective robotic programming. We need to prioritize these steps from the start :
- Feasibility Studies: Leverage digital modeling to assess feasibility and gain precise cycle time estimates.
- Collaborative Planning: Early collaboration between robot integrators and OLP software providers ensures seamless robotic cell configuration.
- Quality Tools: Invest in high-precision tools to maintain repeatable part positioning, critical for efficient automation.
Guarantee Accurate Mechanical and Software Calibrations
Precision is at the core of successful robotic welding programming. Address both mechanical and software aspects:
- Mechanical Calibration: Ensure the robotic cell’s mechanical setup is validated by integrators to achieve high Cartesian accuracy.
- Software Calibration: Develop a digital twin of the robotic cell to precisely align external axes and eliminate post-programming corrections.
Customize Software Solutions for Your Robotic Welding Needs
Adaptable software is crucial to optimize robotic welding programming:
- Collision-Free Simulations: Digital twins facilitate precise, collision-free programming.
- Adjustable Parameters: Enable flexibility by modifying welding parameters for various welding sources and robot brands.
- Post-Processor Customization: Tailor post-processors to reflect the specific requirements of your robotic cell.
Depend on Expert and Responsive Technical Support
Reliable technical support underpins the success of any robotic welding programming initiative:
- Pre-Project Phase: Engage with skilled technical and commercial teams for feasibility studies and equipment selection.
- Implementation Phase: Ensure the installer is proficient in both welding and robotics and capable of software customization.
- Post-Implementation Support: Maintain productivity with a responsive hotline to expedite program creation and scaling.
Train and Empower Programmers in Robotic Welding Techniques
Equipping programmers with the right skills and tools is essential for mastering robotic welding programming:
- Specialized Training: Offer customized sessions to help programmers navigate CAD/CAM tools tailored for welding and robotics.
- Ongoing Support: Provide assistance for programming initial parts to boost confidence and proficiency in using OLP solutions.
Alma: A Leader in Robotic Welding Programming Solutions
Since 1994, Alma has pioneered off-line programming solutions for robotic welding. In collaboration with the “Institut de Soudure”, Alma harnessed its robotics expertise to develop Almacam Weld—a comprehensive, high-performance solution for robotic welding programming. Trusted by manufacturers in over ten countries, Almacam Weld is a benchmark in the industry.
Alma’s partnerships with leading robot integrators and manufacturers ensure advanced solutions tailored to client needs. From initial assessments to skill transfer and user support, Alma provides end-to-end assistance, empowering businesses to excel in mechanical welding industry.