Why is Offline Programming (OLP) essential for benefiting robotized welding
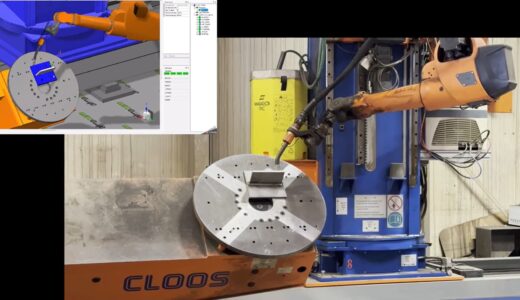
If you are considering investing in a robotic welding cell, you may also be evaluating whether it’s worthwhile to invest in offline robot programming software. Unlike traditional teach pendant programming, offline programming (OLP) allows robots to be programmed graphically in a virtual scene, simulating their movements and refining welding paths before execution. This approach offers numerous advantages and benefits of OLRP that make it an indispensable solution for robotic welding operations.
5 Key benefits of offline robot programming
Increased productivity and reduced downtime
One of the most significant benefits of offline robot programming is the ability to keep production running while programming is done separately. Programming robots via OLP can be up to 10 times faster than using a teach pendant. By working in a virtual environment, manufacturers can create and optimize welding programs without halting production, ensuring robots remain in operation and maximizing uptime.
OLP also facilitates sensing, multi-pass welding, and multi-robot coordination, making it a versatile solution for complex welding tasks. For facilities requiring a high volume of programming, the investment in OLP often has a payback period of about one year.
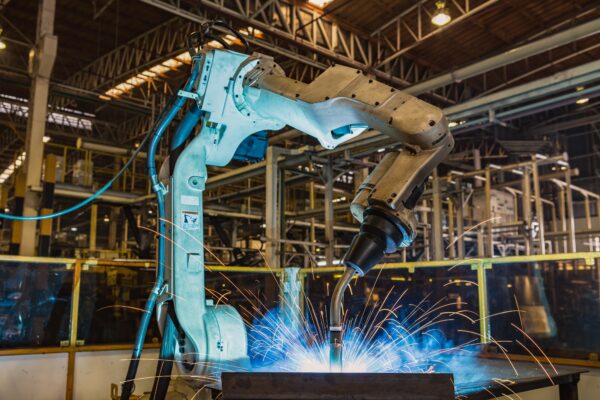
Optimizing production
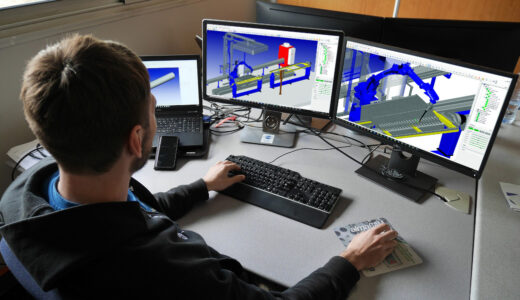
Offline programming enables early validation of welding feasibility. By using realistic simulation tools, manufacturers can:
- Ensure that parts can be welded on the robot before physical production begins.
- Validate CAD-designed tools before they are manufactured.
- Program assemblies as soon as they are designed, without waiting for their physical arrival at the workshop.
- Accurately estimate robot cycle times, helping optimize production planning and scheduling.
Producing small series becomes feasible
For manufacturers producing small series or customized products, Offline Programming enhances flexibility. Features such as duplication, symmetry, and cloning enable rapid adaptation of robotic welding programs, making it easier to accommodate product variations. By reducing programming time, OLP allows robots to be efficiently used for small batch production, increasing profitability.
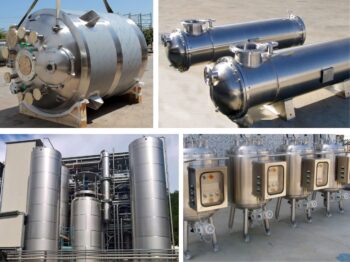
Improved welding quality
Offline programming software optimizes welding angles and penetration, ensuring better weld quality and repeatability. This is particularly critical for industries requiring compliance with Welding Procedure Qualification Record (WPQR) standards. Additionally, multi-pass weld seams become more consistent, reducing defects and rework.
Enhanced safety for operators
Traditional programming on large assemblies can pose safety risks, particularly when operators must work at heights or in hazardous environments. OLP eliminates the need for manual programming near active robots, allowing programmers to work in a comfortable and safe environment in the Methods Office rather than in a noisy and hazardous workshop setting. This also reduces the likelihood of human error, further improving safety and efficiency.
With Almacam Weld, our advanced OLP solution, manufacturers can fully leverage these safety and productivity benefits while streamlining their robotic welding operations.