Continuous laser cutting of coil with DIMECO and Alma: this partnership is on a roll!
Published on 31/05/2021
DIMECO specializes in production systems that use coil. Ever since this family-run business was founded near Besançon, it has always succeeded in combining its leading edge technical expertise with strong growth in international markets. Eight years ago, DIMECO launched an innovative system allowing continuous laser cutting of coil. This solution has been adopted by companies in different sectors (electric equipment, construction, metal furniture, automobile parts, etc.) in several countries. It is controlled using Alma nesting software. The basis for this successful partnership is optimized nesting over considerable lengths, the software’s productivity and its capacity to adapt to each customer’s specific needs.
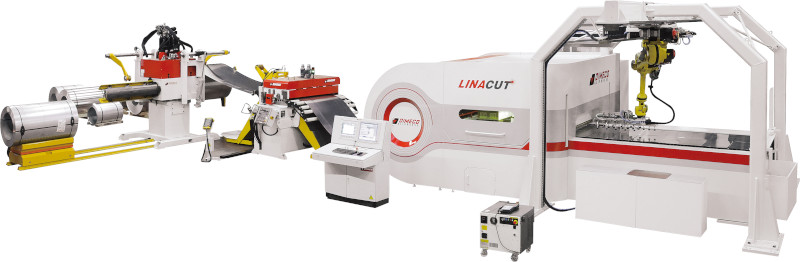
An innovative technology
In 2013 DIMECO chose the Tolexpo trade fair for the world premiere of LINACUT®, its line for continuous laser cutting of coil. Thanks to this innovative process the manufacturer was able to combine the flexibility of laser cutting with the productivity of coil. In concrete terms the installation consists of a decoiling line, a continuous laser cutting module and a module for part unloading and off-cut evacuation. Coils weighing up to 25 metric tons can be fed into the system, with widths up to 2,000 mm. Although the cut thicknesses are usually between 2 and 2.5 mm, the machine is capable of handling thicknesses up to 4 mm.
“The continuous laser cutting technology enables us to produce large volumes of parts in different shapes and sizes completely automatically, with a very low scrap level” explains Thibault Nosbonne, a sales engineer at DIMECO. This is a great improvement compared to punching-nibbling with its tool management constraints, although DIMECO does also produce mixed continuous cutting lines combining laser cutting and punching. For example it can be used to create complex shaped parts with stamped sections. “The other advantage of this continuous process compared to sheet is that it can cut very long parts, exceeding the capabilities of standard laser machines” adds Thibault Nosbonne. What’s more, for companies making their own parts (who are the main users of the LINACUT® system), coil enables them to rationalize production and reduce raw material procurement costs, by grouping the sheet thicknesses and coil widths.
In an automated production process, automatic unloading of parts and scrap is a key issue. A 10 metric ton coil 1,500 mm wide and 1 mm thick is equivalent to more than 270 metal sheets 3 meters long. Of course, the time taken to change a coil is longer than for a single sheet, but you only have to do it once. Combine this with automated unloading systems and you get unbeatable autonomy. Thanks to its conveyors, robots, gripping and palleting systems, etc. DIMECO proposes several processes combined with the machine to evacuate, sort and stack parts. Each application is perfectly adapted to the customer’s specific needs.
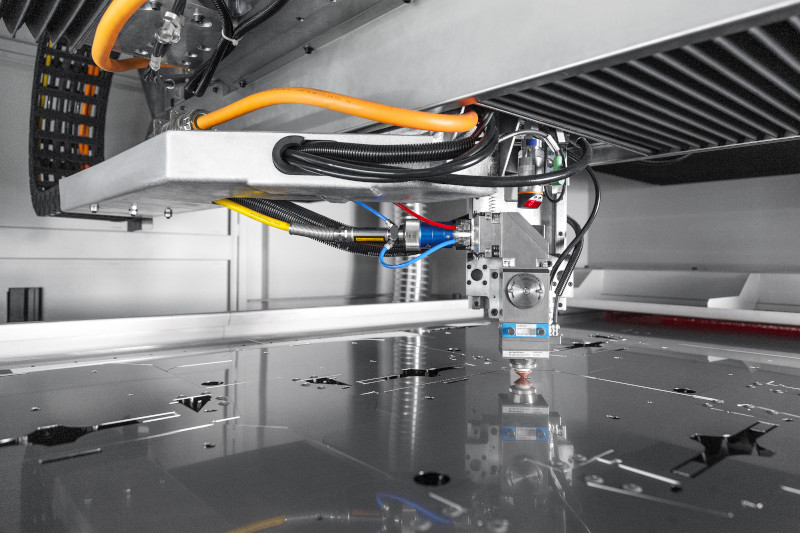
The nesting software, a key component of the LINACUT® solution
To maximize productivity you must use an ad hoc nesting software for continuous cutting of long coils. This is why from the very beginning DIMECO chose to sell its LINACUT® machines with the Alma software embedded, both in France and abroad. It decided that this was the best software, not only to automatically nest parts of any shape, but also to reduce programming times thanks to its intuitive automated functioning.
Extensive work was required to adapt the Alma nesting algorithms to the specificities of LINACUT® machines. “The software adapts perfectly to the operating principles of our machine, making it possible to achieve excellent material utilization” confirms Thibault Nosbonne. “Nevertheless it is always necessary to have a discussion with the user to determine the best cutting strategy depending on their type of production.”
Another reason for choosing the Alma solution was the vendor’s capacity to develop customer-specific solutions, in close collaboration with the machine’s manufacturer. Apart from the post-processor dedicated to the machine, this is particularly useful for managing the different part evacuation systems that DIMECO has integrated into its continuous cutting line. In concrete terms, the Alma software sends the gripping system the exact position of each part and the part removal location. However each customer has their specificities and so the control of palleting must always be adapted.
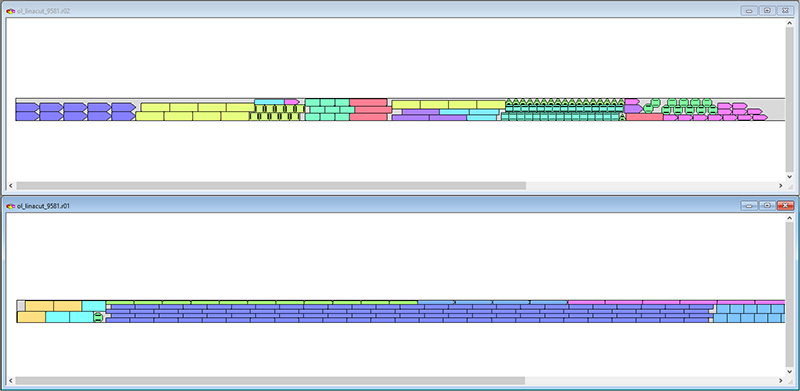
Close collaboration between the manufacturer and the software vendor
In this context, the end-users of the software are always trained by Alma. For practical purposes a DIMECO engineer trained to use the software is dedicated to LINACUT® customer support once the software has been installed.
Collaboration between the software vendor and the machine manufacturer is very important, for both initial development of the solution and assessment of each customer’s needs. “The level of maturity of our partnership with Alma is excellent” notes Thibault Nosbonne. “We work very efficiently with the Alma application engineers, who have fully understood the key aspects of the LINACUT® solution.”
Moreover, enhancements of the software are currently being tested, in particular to restart cutting in the middle of a nesting in the right place immediately, e.g. after a power failure on the machine. This constant search for productivity gains is made possible by a close partnership and shared long-term vision.